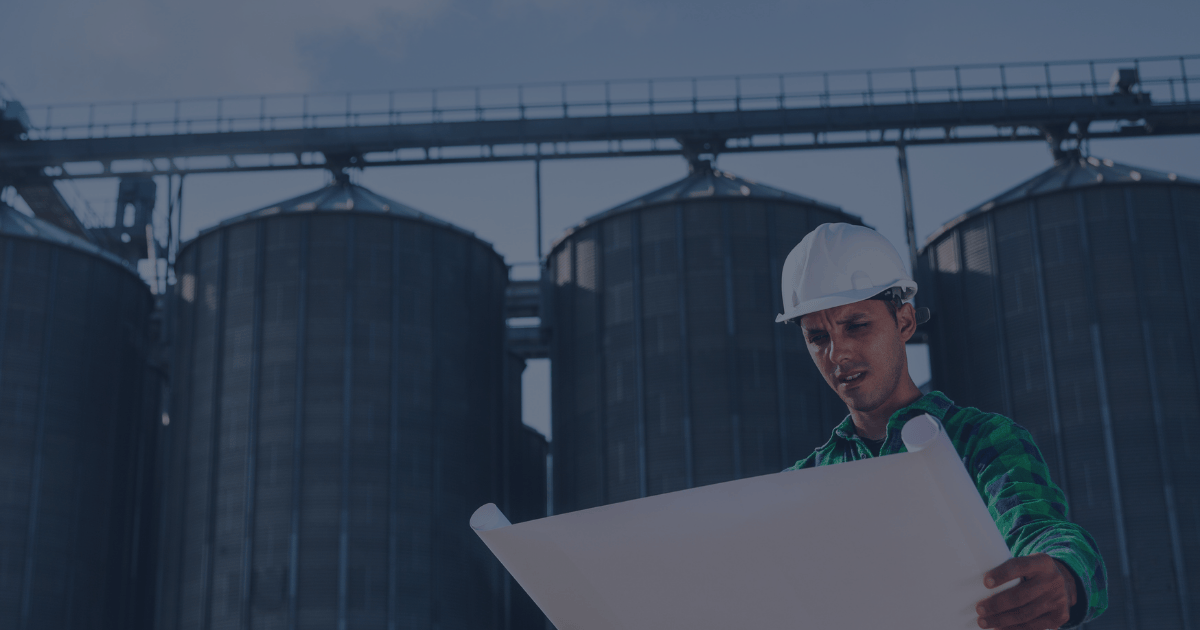
Why Dynamic Scheduling Beats Static Manufacturing Plans
Why Production Scheduling Software Alone Falls Short in Modern Manufacturing
Ask most manufacturers how they build their weekly production schedule and you’ll hear familiar answers, a spreadsheet, a static ERP module, or a manual Gantt chart buried in the MES. That might have worked when demand was predictable and changeovers happened like clockwork. But in today’s world of shifting priorities, labor variability, and supply chain disruptions, static scheduling tools create hidden delays, scheduling conflicts, and operational blind spots.
This article explains how dynamic, AI-enabled scheduling elevates traditional production planning giving manufacturers flexibility, speed, and clarity when conditions change by the hour, not the month.
Why Static Scheduling Breaks Down in Modern Operations
Production scheduling software was originally designed to handle linear, predictable manufacturing environments. These tools excel at locking in weekly or monthly production plans, aligning procurement and staffing with known demand. But static schedules aren’t built to flex in real time. When disruptions happen, the gap between plan and reality widens fast.
Consider this typical scenario. A food processing plant builds its schedule Monday morning based on labor availability, material inventory, and planned maintenance. By Wednesday:
- A supplier delay means raw materials won’t arrive on time.
- A key production line experiences unexpected downtime.
- A priority customer shifts an order, demanding earlier delivery.
The schedule? Still frozen in last Monday’s reality. The planner must manually scramble to rebuild the week midstream, often working outside the ERP or MES in disconnected spreadsheets.
These gaps aren’t theoretical. Deloitte reports that 62 % of manufacturers still rely on static scheduling systems to manage highly dynamic shop-floor realities, despite widespread digital transformation efforts (Deloitte, 2024).
What “Dynamic” Scheduling Really Means
Dynamic scheduling moves beyond static plans and reactive adjustments. It connects live shop-floor data - machine states, labor availability, material flow - to scheduling engines that adapt automatically. When something changes, the plan updates. Not next week, but now.
What distinguishes dynamic scheduling from static tools isn’t just speed. It’s how decisions are made. Instead of chasing yesterday’s bottlenecks, dynamic systems continuously weigh:
- What orders are prioritized right now?
- What capacity is realistically available?
- How will this choice ripple downstream?
This shift allows manufacturers to stay aligned to business goals, not just operational constraints, even as those constraints evolve hour by hour.
How AI Powers Dynamic Scheduling
AI doesn’t make scheduling decisions in a vacuum. It amplifies human judgment by analyzing constraints, surfacing trade-offs, and suggesting optimized paths forward faster than any planner could model manually.
Key AI capabilities include:
- Scenario modeling: Running thousands of permutations to find the best sequence under current constraints.
- Constraint balancing: Weighing labor, equipment, material, and energy availability in real time.
- Learning from overrides: Adapting recommendations over time based on how humans adjust them.
This isn’t about replacing the scheduler. It’s about giving them superpowers. Moving from firefighting to proactive optimization.
Use Cases: Where Dynamic Scheduling Delivers Impact
To illustrate, consider two real-world scenarios:
Scenario 1: Mid-Shift Line Failure
A key packaging line goes down mid-shift. In static environments, this triggers a scramble. Planners manually re-sequence jobs, shift labor, and notify downstream teams all while production slows.
With dynamic scheduling, the system detects the failure in real time, recalculates the optimal production sequence across all remaining assets, and updates shift plans instantly. Downtime’s impact is minimized, and throughput is preserved without guesswork.
Scenario 2: Last-Minute Customer Priority Change
A major customer moves up a delivery date. The legacy plan can’t accommodate without overtime or disruption. A dynamic scheduler models alternatives within minutes, shifting low-priority runs, reallocating labor, and highlighting potential trade-offs in cost or lead time. The planner approves the best-fit option, confident it reflects the latest reality.
Beyond Efficiency: Why This Matters
Dynamic scheduling delivers more than smoother production. It reshapes how organizations operate:
- Higher OEE: Less downtime cascades from disconnected plans.
- Reduced waste: Smarter sequencing cuts changeovers and material loss.
- Stronger collaboration: Cross-functional teams trust the plan reflects reality, not assumptions.
- Improved delivery performance: Agility reduces expedite costs and strengthens customer confidence.
Resilience isn’t a buzzword. It’s a competitive edge. Dynamic scheduling makes operations less brittle and more responsive when the unexpected hits.
Conclusion: Why Agility Wins in Modern Manufacturing
Manufacturers still clinging to static scheduling risk running operations that look efficient on paper but crumble under real-world volatility. Dynamic scheduling bridges that gap, aligning plans with reality in real time, empowering humans with faster, clearer options, and turning agility from aspiration into practice.
At NTWIST, we help manufacturers evolve from static to dynamic operations because faster, better decisions drive more than efficiency, they drive resilience.
Explore Dynamic Scheduling Solutions
References
Deloitte. (2024). Smart Manufacturing and the AI Talent Multiplier. Retrieved from https://www.deloitte.com/us/en/services/consulting/articles/smart-factory-mes.html
MachineMetrics. (2024). How Manufacturing Production Scheduling Software Solves Shop Floor Challenges. Retrieved from https://www.machinemetrics.com/blog/manufacturing-production-scheduling-software