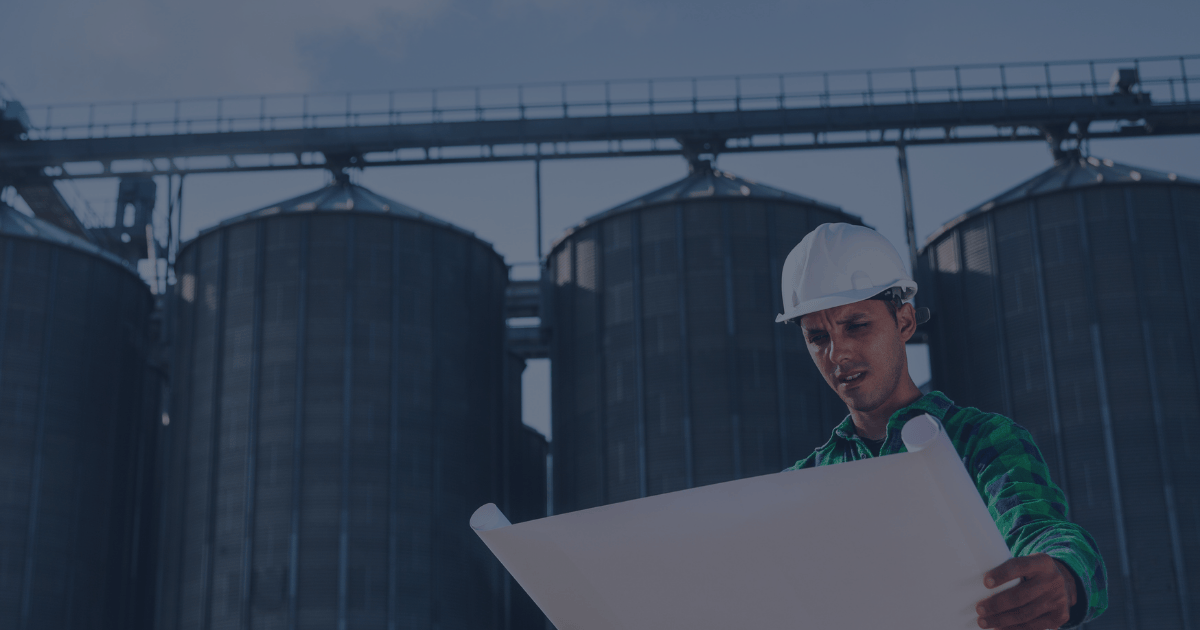
AI in Mining & Manufacturing: Why It’s Built to Help, Not Replace
AI isn’t coming to take your job. It’s coming to give you back your time, your judgment, and your control. The question isn’t whether you’ll still wear the hard hat, it’s whether you’ll let AI help you wear it better.
The Noise vs. The Reality
Spend five minutes on LinkedIn and you’ll find someone warning about AI automating jobs out of existence. Charts, think-pieces, and headlines love to forecast a future where control rooms are dark, trucks drive themselves, and schedulers are replaced by algorithms.
It makes for great engagement. But if you step onto any mine site or factory floor today, the reality is far less dramatic and far more human.
AI isn’t coming to take your job. It’s coming to help you do your job better.
What’s really being automated isn’t people, it’s wasted time, guesswork, and reactive firefighting.
According to LinkedIn’s Future of Work report, 56 % of roles could face AI-driven change, but 74 % of executives believe AI will ultimately create more opportunity than risk (LinkedIn Economic Graph, 2023).
Humans and AI: A Division of Labor That Works
The real future isn’t humans versus AI. It’s humans and AI, each focused on what they do best.
What Humans Do Best | What AI Does Best |
---|---|
Navigate trade-offs and nuance | Process massive, messy datasets |
Use intuition and experience | Detect patterns too fast to see |
Build relationships and trust | Run scenarios in seconds |
Prioritize conflicting needs | Balance variables with precision |
Make judgment calls | Deliver options, not absolutes |
When AI and humans work together, humans ask better questions and AI provides faster answers. Decisions get made sooner, with less stress, more clarity, and fewer surprises.
How This Looks on the Ground
Imagine a manufacturing planner. Her day used to start with a messy whiteboard, a dozen sticky notes, and an inbox full of last-minute "can we squeeze this in" requests.
When equipment failed mid-shift or an urgent customer order landed, she would spend hours manually reshuffling jobs, calling maintenance, chasing operators, and hoping she hadn’t missed a constraint buried in the ERP.
With AI, her day changes:
- The system flags when downtime risks a delivery date.
- It suggests alternate sequences before she even gets out of her chair.
- It shows the ripple effect, this change adds two hours, shifts labor, increases energy costs.
- It asks, "Do you want to approve this plan or adjust the priorities?"
She’s still the decision-maker. Now she’s making decisions with a map, not a guess.
Mining Is No Different
Picture a dispatcher at a mine. He used to rely on shift reports, whiteboards, and verbal updates to decide which trucks went where. When a shovel broke down or a rainstorm hit the haul roads, his mental model had to adjust on the fly.
One mistake, sending too much hard ore to the mill or forgetting a blending target, and the entire operation paid the price for days.
With AI helping:
- Live data shows what’s happening across pit, plant, and stockpile.
- Recommendations adapt in real time to constraints, equipment downtime, moisture, grade variability.
- The system doesn’t order him around, it says, "Here’s the fastest route back to stability. Here’s why."
McKinsey reports that mining companies achieving operational excellence through AI coordination see greater efficiency, reduced costs, and faster adjustments to variable conditions (McKinsey, 2024).
AI Isn’t Magic. It’s a Better Toolset.
AI isn’t some black box making perfect decisions. It’s software doing what spreadsheets and dashboards can’t, connecting dots fast enough to help you act while the window is still open.
What does that mean in practical terms?
Without AI | With AI |
---|---|
Hours spent reworking plans | Scenarios updated in minutes |
Blame games over missed targets | Shared visibility reduces conflict |
Gut-feel overrides | Data-backed decisions gain trust |
Delays stack up silently | Constraints flagged proactively |
Stress drives decisions | Information drives decisions |
The best AI doesn’t replace human judgment. It gives it better inputs.
Why People Still Matter Most
AI doesn’t understand your customer’s quirks, your crew’s strengths, or your shift culture. It doesn’t know that the mill runs smoother with that one operator on nights.
It can tell you, "This plan maximizes throughput." But only you can say, "That plan fits our people and our priorities."
AI can’t lead. It can’t mentor. It can’t take accountability. It can only help you move faster toward what you already know matters.
What Changes, and What Doesn’t
What changes with AI?
- Less time firefighting
- Faster clarity when things go wrong
- Better alignment across teams
- More confidence in decisions
What doesn’t change?
- The need for human oversight
- The responsibility to lead
- The value of experience and expertise
AI is the tool. Humans still write the playbook.
What This Means for the Future
The jobs at risk aren’t hard hats. They’re the inefficiencies we’ve lived with too long:
- Manual workarounds no one trusts
- Siloed systems that don’t talk
- Decisions made too late to matter
The companies that thrive won’t be the ones with the most AI. They’ll be the ones where humans and AI operate like a team, aligned, agile, and able to solve problems before they spiral.
That’s not science fiction. That’s already happening, in mines, mills, and factories where people see AI not as competition, but as a collaborator.
The World Economic Forum’s Lighthouse Network highlights how factories leveraging advanced technologies achieve double-digit gains through better coordination, not just automation (World Economic Forum, 2025).
Final Thought
AI isn’t here to take your job. It’s here to help you keep your sanity, your schedule, and your ability to go home on time.
Coordination, not technology, remains the hardest problem. And the people who solve it will always have a place on the team.
Curious how you can integrate AI into your operations? Click below and explore solutions that work.
References
Deloitte. (2024). Smart Manufacturing and the AI Talent Multiplier. Deloitte Insights. https://www.deloitte.com/us/en/services/consulting/articles/smart-factory-mes.html
LinkedIn Economic Graph. (2023). Future of Work Report: AI at Work. LinkedIn Corporation. https://economicgraph.linkedin.com/research/future-of-work-report-ai
McKinsey & Company. (2024). Mining for Operational Excellence. McKinsey & Company. https://www.mckinsey.com/capabilities/operations/our-insights/mining-for-operational-excellence
World Economic Forum. (2025). Advanced Technologies Help Manufacturing Factories Scale Innovations. World Economic Forum. https://www.weforum.org/impact/advanced-tecnologies-manufacturing-factories-scaling-innovations/