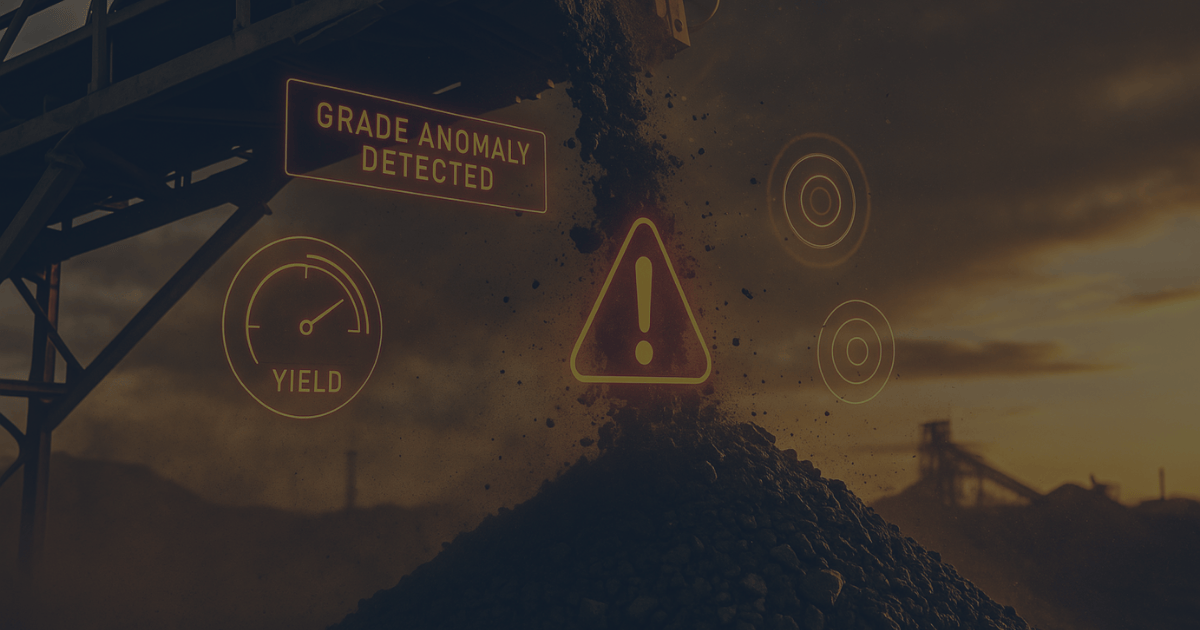
Stop Ore Loss: Optimize Stockpiles and Prevent Misclassification
When Good Ore Goes to Waste: How to Optimize Stockpiles and Prevent Misclassification
At NTWIST, we’ve worked with mining operations around the world, and one pattern emerges repeatedly: valuable ore is misclassified, misrouted, and mismanaged long before it ever reaches the mill. In high-throughput, open-pit operations, this misclassification often ends in one place - the wrong stockpile.
This isn’t just a process inefficiency. It’s value destruction. Recoverable ore ends up as waste, metallurgical models get skewed, and downstream systems suffer from poor feed quality. We’re here to break down why this happens, how much it’s costing, and what you can do to fix it.
The True Cost of Ore Misclassification
Ore misclassification occurs when inaccurate blast movement modeling, improper dig boundaries, or outdated geological assumptions lead to high-value material being routed as low-grade - or worse, waste. This issue is especially prevalent in open-pit mines where blast movement isn't actively corrected using offset vectors or digital reconciliation models.
According to a study published on ResearchGate, failing to account for blast-induced movement can cause up to 20% ore loss and 20% misclassification in copper operations, severely degrading mill feed accuracy and grade forecasting (ResearchGate, 2018).
When that material gets dumped on the wrong stockpile, it's essentially lost. You may never reclaim it. Worse, your entire production chain - from crushing and blending to metallurgy and reconciliation - now operates off bad data.
Stockpile Optimization Requires Real-Time Intelligence
Many mines rely on truck tags, shovel guidance systems, and grade control drilling to assign material. But in practice, these systems often operate in isolation - failing to create a continuous, intelligent ore tracking loop. The result is that dig blocks are treated statically, with little accounting for blast movement, operator override, or equipment-driven routing errors.
As Propeller Aero explains, stockpile accuracy and accountability improve dramatically when operations transition from manual surveys to automated tracking systems, such as drone-based volume scanning, 3D dig block modeling, and real-time dispatch data (Propeller, 2023).
But digitizing stockpiles isn’t enough - you need to integrate that intelligence upstream. AI-driven platforms like NTWIST’s nGeoMet-AI pair geological models with blast offset correction and dispatch feedback loops, enabling mines to dynamically adjust material classification and stockpile assignments on the fly.
Why Most Mines Misclassify
Let’s be clear: no operation sets out to throw away valuable ore. But most misclassification happens because systems aren’t connected - or because geological models lag behind operational decisions. Common causes include:
- Blast movement ignored: Misplaced dig lines due to uncorrected displacement
- Over-simplified classification: Dig blocks defined with wide grade bins, lacking resolution
- Disconnected systems: Dispatch, grade control, and reconciliation don’t share live feedback
This means a truckload flagged as “marginal” could contain pockets of high-grade ore - and once dumped, it’s practically invisible.
The Solution: AI-Powered Routing and Feedback
To stop stockpile misallocation, you need a system that sees beyond static classifications. NTWIST’s approach uses predictive models trained on historical orebody performance, blast displacement behavior, and live operational data. With these inputs, AI can recommend not just where to dig, but where to send each truck - in real time.
This routing intelligence is then fed back into downstream models, continuously improving reconciliation accuracy and enabling proactive blending. The result? Higher mill head grades, fewer recovery losses, and tighter alignment between geology and operations.
3 Things You Can Do Today
- Start measuring the gap: Compare expected vs actual mill feed grade and identify stockpile contributors.
- Audit your blast model assumptions: If you’re not accounting for movement, you’re already behind.
- Connect your systems: If your dispatch, geology, and reconciliation teams use different platforms - close that gap.
Conclusion: Misclassified Ore is Not Just a Mistake - It’s a Metric
At NTWIST, we treat ore misclassification and stockpile misallocation as KPIs worth tracking. If your systems aren’t catching these losses in real time, you’re leaving value in the wrong place - and it may never come back.
The good news? With the right intelligence, you can route smarter, reclaim value, and restore confidence in your production data. And we’re here to help you lead that change.
Explore Mine-to-Mill Optimization
References
ResearchGate. (2018). Minimizing Mining Dilution, Ore Loss and Misclassification by Accounting for Blast Movement. Retrieved from https://www.researchgate.net/publication/327592841_Minimizing_Mining_Dilution_Ore_Loss_and_Misclassification_by_Accounting_for_Blast_Movement
Propeller Aero. (2023). Top 5 Workflows for Mining and Aggregates. Retrieved from https://www.propelleraero.com/blog/top-5-mining-aggregates-workflows/